"Revolutionizing Ammunition Manufacturing: Unleash Unparalleled Precision and Efficiency with Our State-of-the-Art Automatic Bullet Casing Production Systems. Engineered for Excellence, Crafted for Consistency, Redefining the Future of Firearms Technology."
“Embark on a New Era of Ammunition Innovation: Our Automatic Bullet Casing Production Solutions Redefine Manufacturing Excellence. Meticulously Engineered for Unprecedented Precision, Efficiency, and Consistency, Our Cutting-Edge Systems Ensure Every Casing Meets the Highest Standards of Quality. From Raw Material Handling to Advanced Machining, Our Technology Paves the Way for a Seamless and Regulatory-Compliant Production Process. Elevate Your Ammunition Manufacturing to Unmatched Heights with Our State-of-the-Art Solutions, Where Craftsmanship Meets Automation for a Future Forward in Firearms Manufacturing.” This machine streamlines the production process, ensuring high-quality and consistent bullet casings for use in firearms. Here is a more detailed description of the key components and processes involved in an automatic bullet casing production machine:
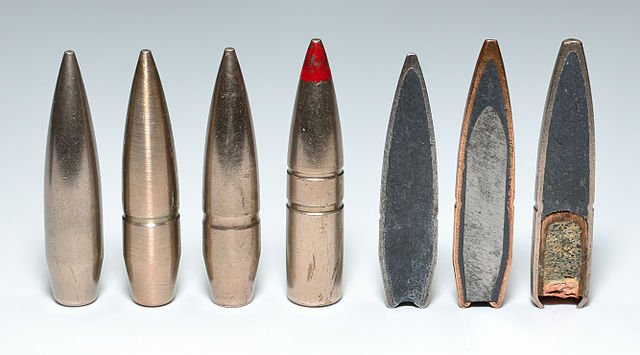
Raw Material Handling
- The machine is equipped with a feeding system, such as a magazine or hopper, to hold raw materials. Common materials include brass or other alloys suitable for bullet casings.
- Vibratory feeders or conveyor systems ensure a continuous and controlled supply of raw materials to the production line.
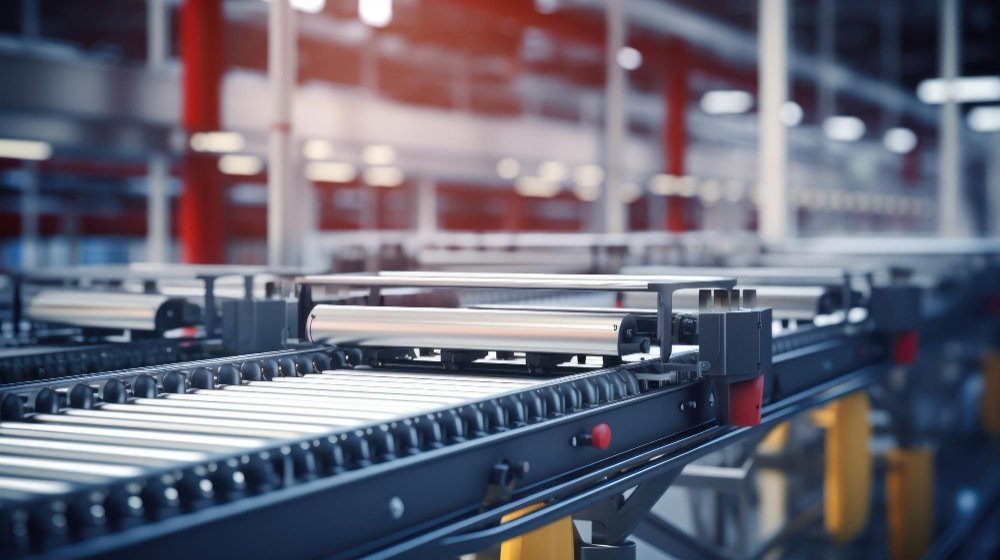
Material Preparation
- A cutting mechanism, such as shearing equipment, is employed to cut the raw material into the required length for casings.
- Surface cleaning or polishing stations are integrated to remove any imperfections or contaminants from the raw material.
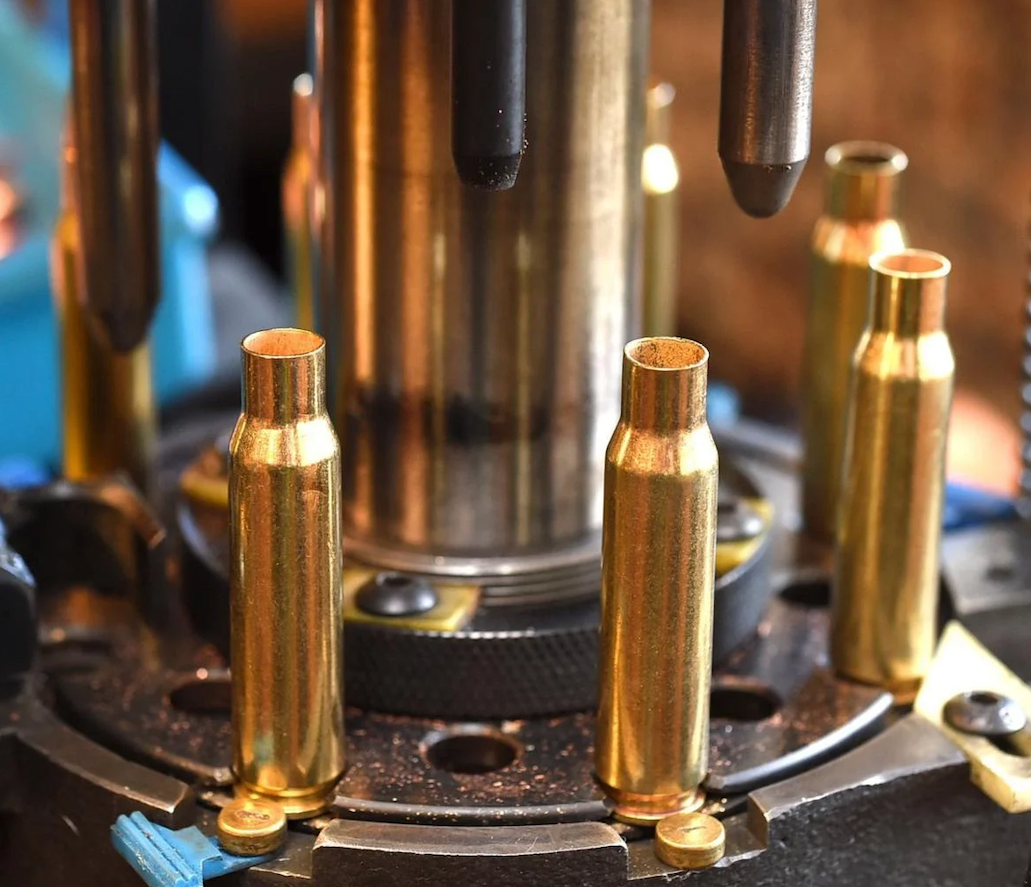
Forming and Shaping
- Precision forming dies are utilized to shape the casings according to specific dimensions.
- Hydraulic or mechanical presses apply controlled force to the material, shaping it into the desired casing form.
- Lubrication systems may be in place to reduce friction and facilitate the forming process.
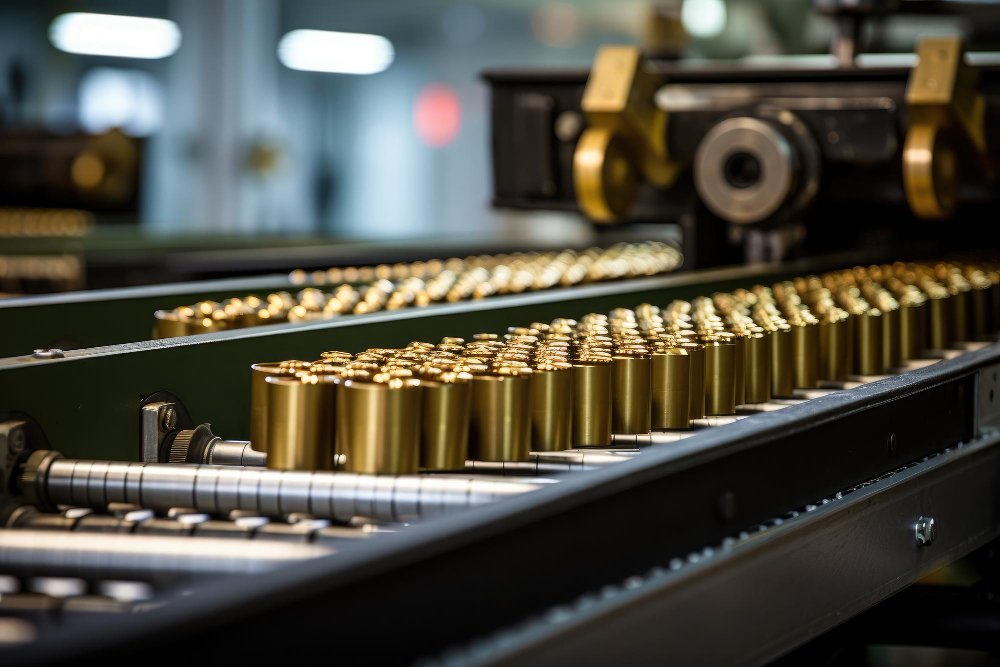
Machining and Processing
- CNC (Computer Numerical Control) machines are employed for precision machining of the casing, ensuring accurate dimensions.
- Drilling and milling stations create necessary features such as primer pockets and flash holes.
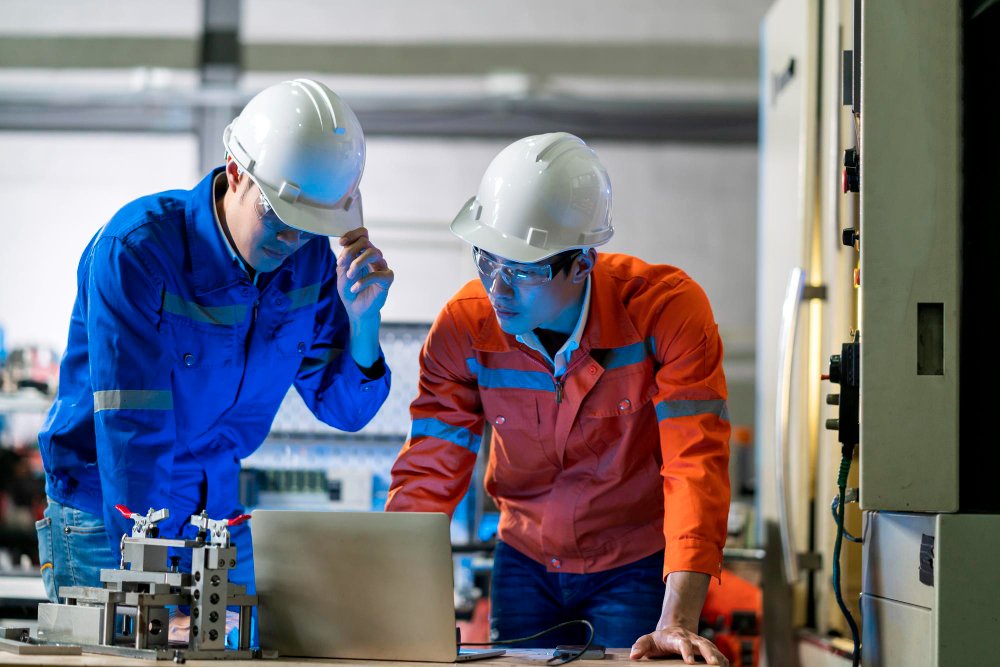
Quality Control
- Vision systems or sensors inspect each casing to ensure compliance with quality standards.
- Faulty casings are identified, and a rejection mechanism is in place to remove them from the production line.
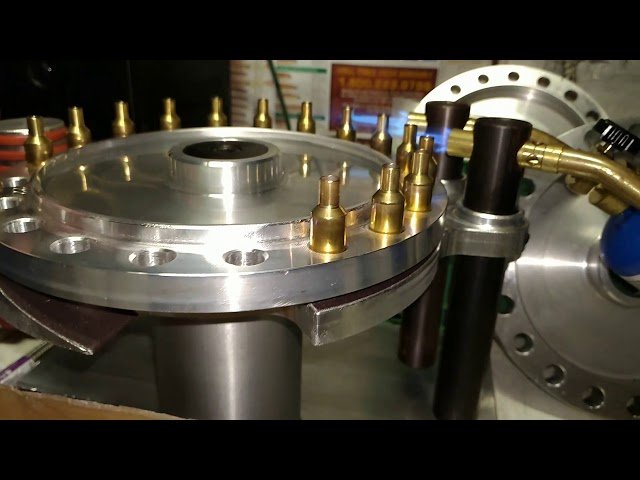
Heat Treatment
- Casings may undergo heat treatment in an oven or chamber to enhance their strength and durability..
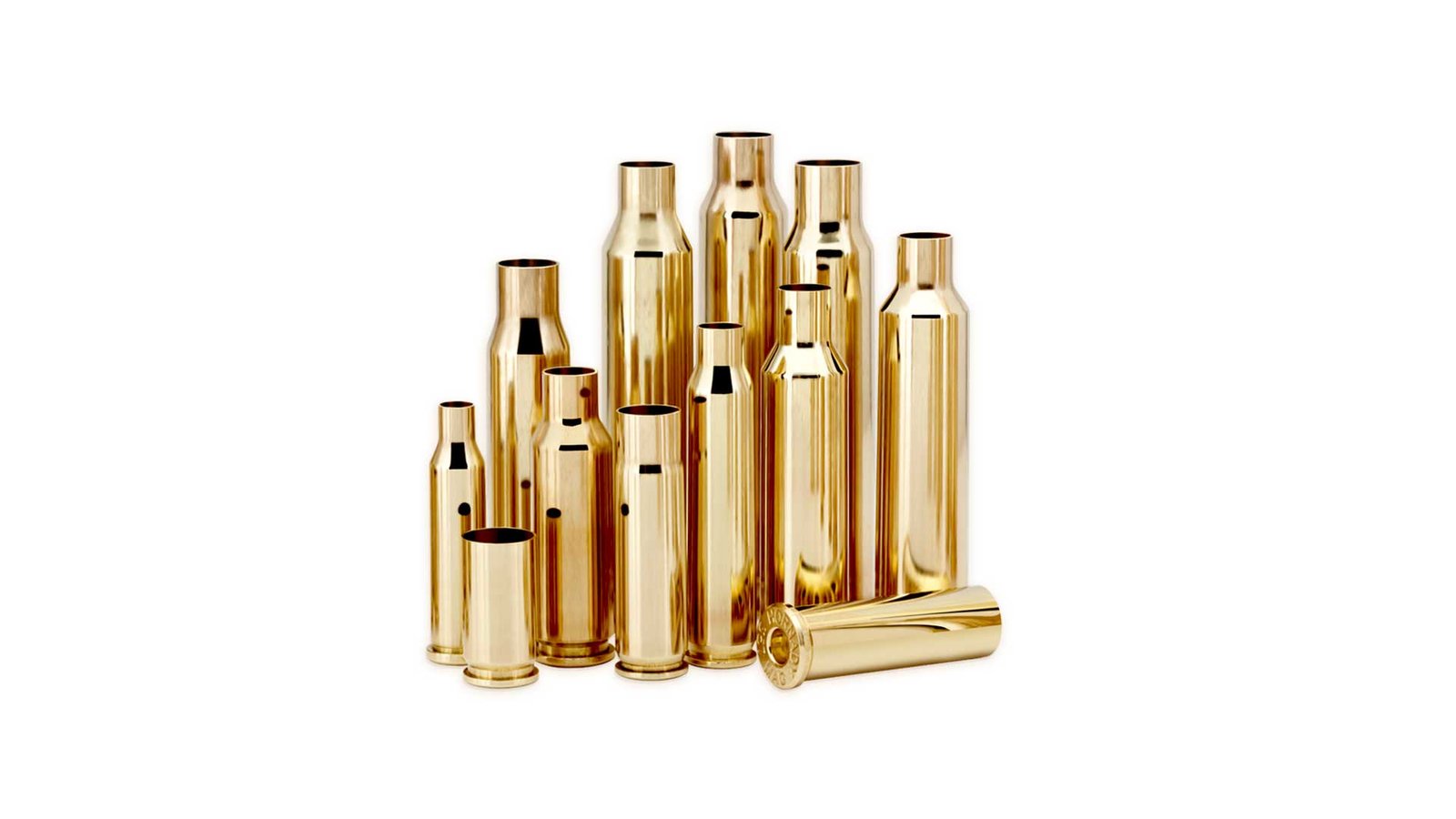
Coating or Finishing
- A coating application system may be integrated to provide corrosion resistance or for aesthetic purposes.
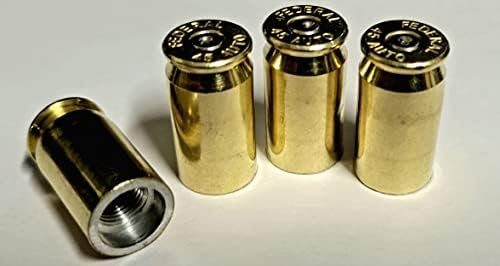
Marking and Identification
- Laser marking or engraving systems add necessary markings and identification information to each casing.
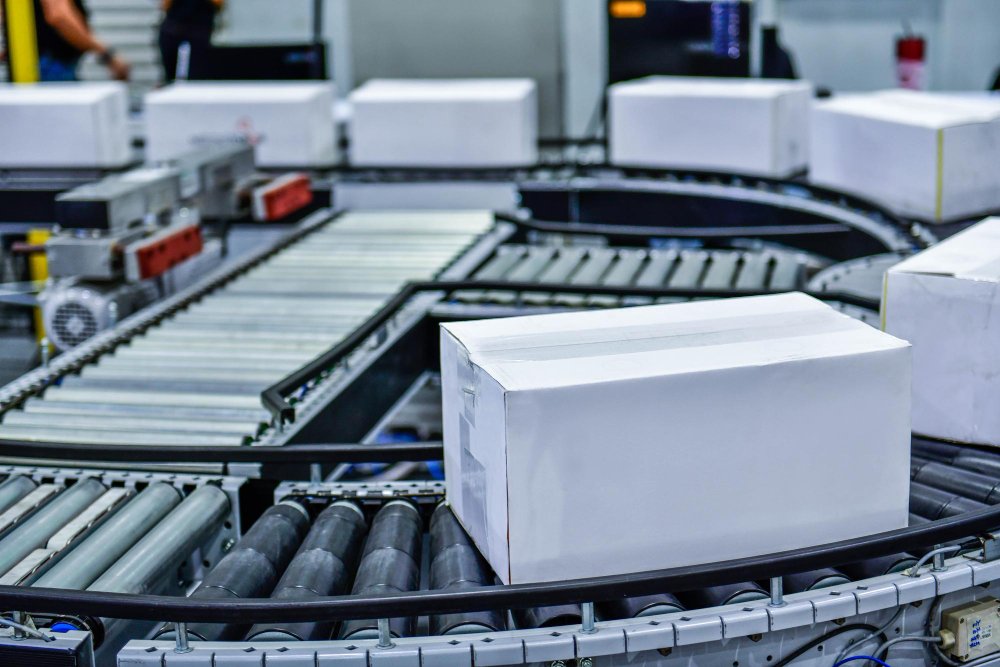
Packaging
- An automatic packaging system sorts and packs the finished casings for distribution.
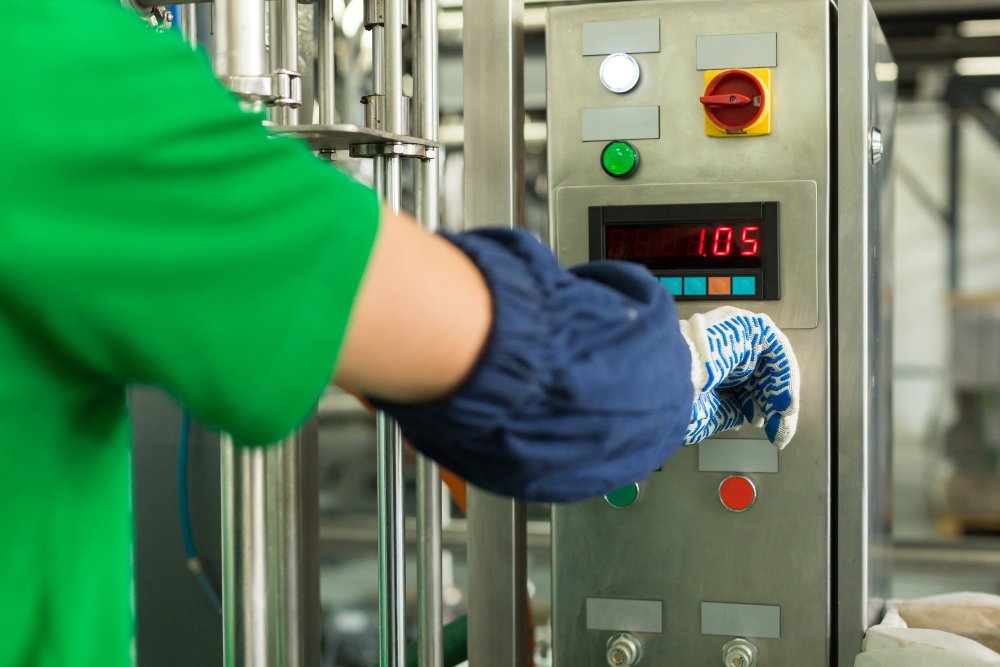
Safety Features
- The machine is equipped with safety features such as emergency stop buttons, safety interlocks, and physical barriers to protect operators during operation.
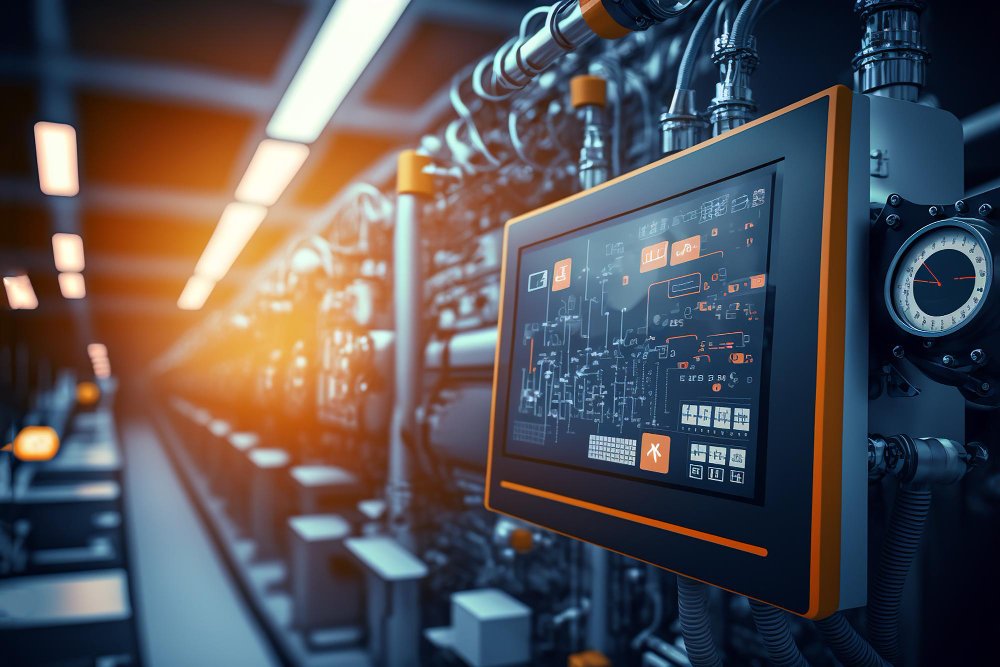
Control System
- A sophisticated control system, often based on a Programmable Logic Controller (PLC) or computer-based control, manages the entire production process. Human Machine Interface (HMI) allows operators to monitor and control the machine.
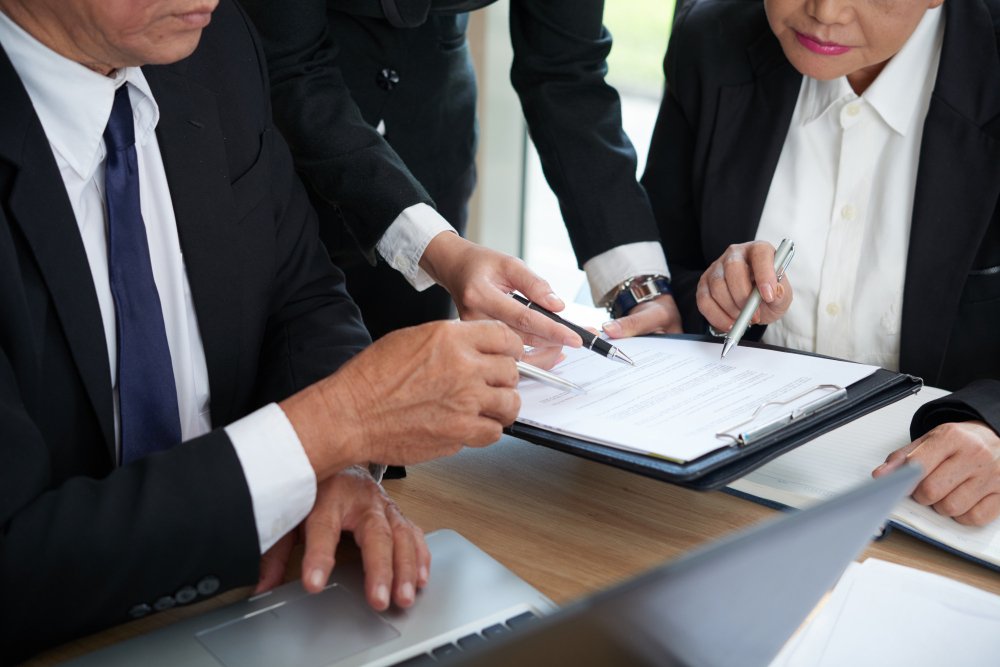
Regulatory Compliance
- The design and operation of the machine comply with all relevant local, state, and federal regulations governing ammunition production.
This automatic bullet casing production machine represents a highly engineered and automated system that combines precision, efficiency, and safety to meet the stringent requirements of ammunition manufacturing.
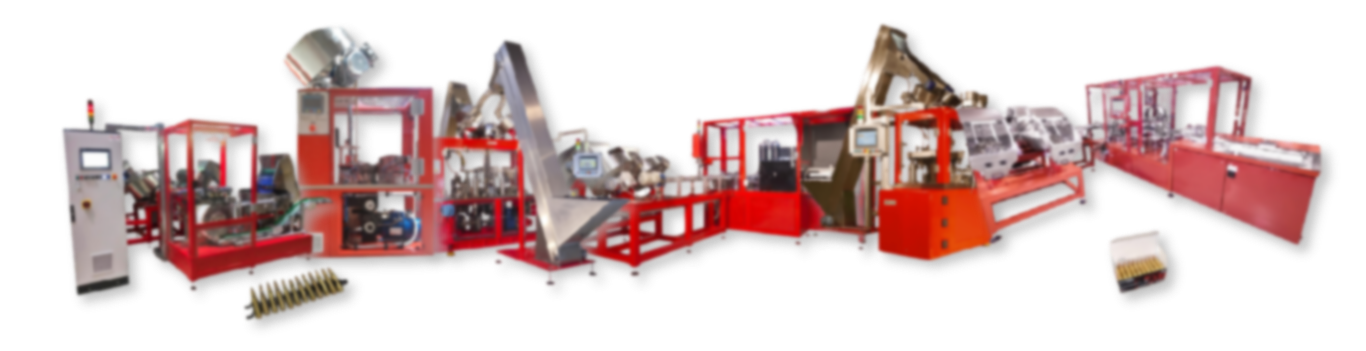